MIG vs TIG Welding: Which One to Choose?
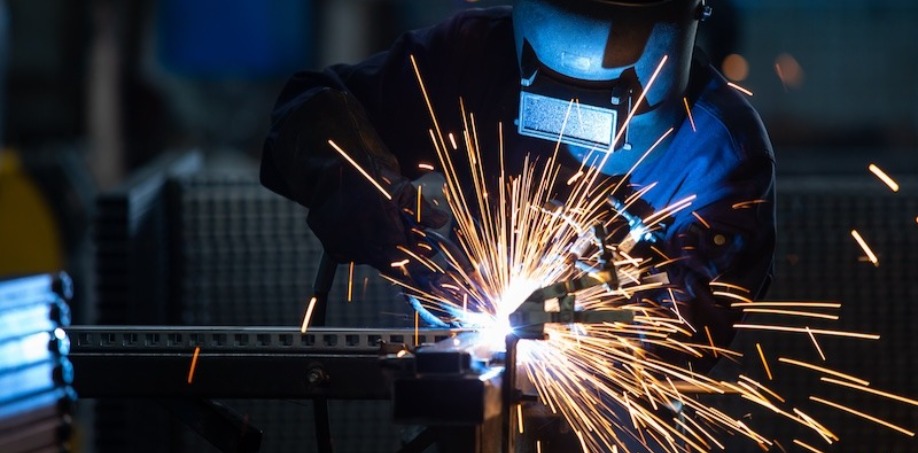
Welding is one of the most crucial techniques used to join metal parts. Whether you're an experienced welder or just starting out, choosing the right welding method is key to ensuring the quality, strength, and appearance of your finished product. Two of the most common welding methods are MIG welding and TIG welding. While both are used to join metal parts, they have distinct characteristics that can affect the outcome of your project. In this blog, we’ll explore the differences between MIG and TIG welding, their uses and applications, and how to decide which one is right for your needs.
What is MIG Welding?
MIG welding, which stands for Metal Inert Gas welding, is a widely used method for joining metals. It is often referred to as Gas Metal Arc Welding (GMAW). MIG welding uses a shielding gas, typically a mixture of argon and carbon dioxide, to protect the molten weld pool from contamination by atmospheric gases. One of the most appealing aspects of MIG welding is its speed and ease of use. It’s a semi-automatic process, meaning that the welder only needs to focus on guiding the welding gun while the machine automatically feeds the electrode wire. This makes MIG welding an excellent choice for both beginners and professionals working on large-scale projects.
MIG Welding Applications
- Thicker Materials: MIG welding excels at working with thicker materials like mild steel and cast iron, making it perfect for construction and automotive industries.
- High-Volume Production: Due to its speed, MIG welding is commonly used in manufacturing environments where large quantities of welds need to be made in a short amount of time.
- Heavy Duty Jobs: MIG welding is ideal for heavy-duty applications where strength and durability are critical, such as structural welding and repair work on industrial machinery.
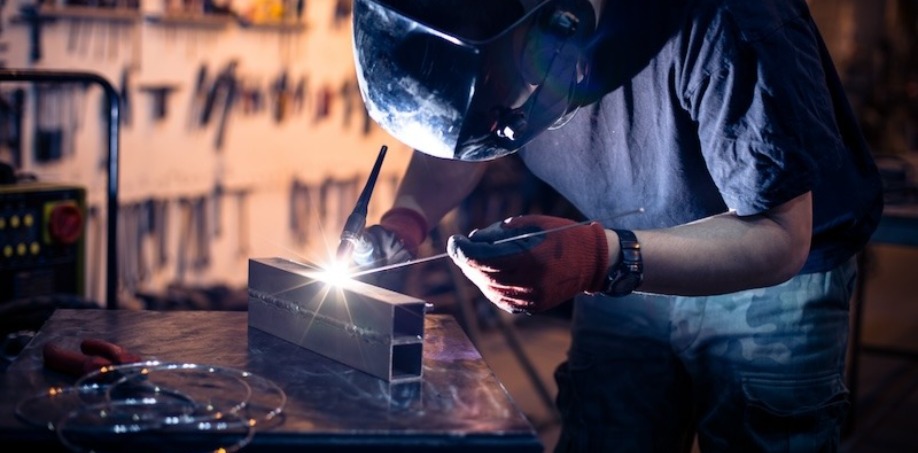
What is TIG Welding?
TIG welding, which stands for Tungsten Inert Gas welding, is another popular welding method. Unlike MIG welding, TIG uses a separate filler rod to supply the material needed to create the weld. TIG welding also utilizes an inert gas, usually argon or helium, to protect the weld pool and prevent oxidation. TIG welding is known for its precision and cleanliness. It allows the welder to have more control over the process, making it perfect for applications that require intricate work and a high-quality finish. Unlike MIG welding, TIG welding requires the welder to manually feed the filler rod while simultaneously controlling the torch, which can be challenging for beginners but results in a higher-quality weld.
TIG Welding Applications
- Thin Metals: TIG welding is often used in industries where precision is essential, such as the aerospace and medical industries, where thin, delicate materials are common.
- Non-Ferrous Metals: TIG welding is the preferred method for joining aluminum, copper, and other non-ferrous metals, which require the precision and control that TIG provides.
- Artistic and Decorative Work: TIG welding is also used in artistic projects where the appearance of the weld matters, such as in artwork or high-end furniture fabrication.
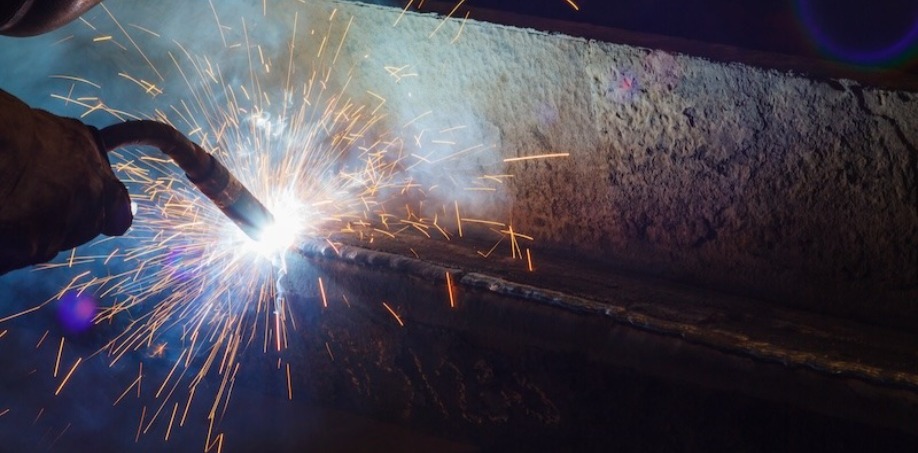
What is the Difference Between MIG and TIG Welding?
Both MIG and TIG welding are valuable techniques, but they have significant differences that can influence which method is best for a particular project. Let’s break down some of the key differences between the two:
Power Source: MIG welding uses a DC (direct current) power source, making it ideal for thinner materials and reducing weld splatter while providing a stable arc for reliable welding. TIG welding, on the other hand, can utilize either DC or AC (alternating current) power sources, with AC being particularly beneficial for welding metals like aluminum, as it assists in cleaning the metal surface during the welding process.
Electrode: In MIG welding, the electrode is consumable, melting to become part of the weld joint, whereas in TIG welding, the electrode is non-consumable; the tungsten electrode delivers the electrical charge while the filler material is added separately using a rod.
Welding Speed: MIG welding is faster than TIG welding because the machine automatically feeds the filler material, enabling the welder to work quickly and complete large jobs efficiently. TIG welding is slower due to the manual feeding of the filler material and the need to control both the electrode and the torch.
Weld Quality: MIG welds are durable and strong but generally less aesthetic than TIG welds, making MIG welding ideal for thicker materials where appearance is less critical. TIG welding produces cleaner, more aesthetic welds, making it perfect for delicate, thin materials requiring precise, high-quality joints.
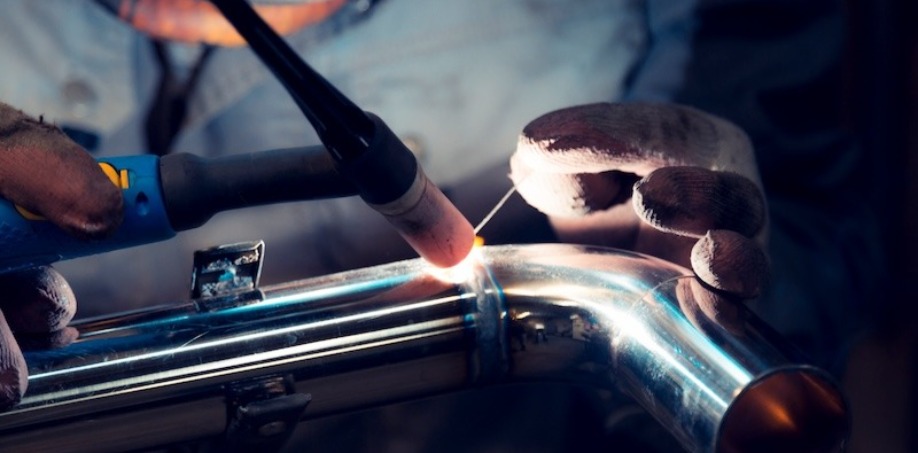
MIG vs TIG Welding: Which One to Choose?
Now that you understand the key differences between MIG and TIG welding, the next question is: how do you decide which method to use for your project? Here are some factors to consider:
Type of Metal
- MIG Welding: Best suited for thicker materials like mild steel, cast iron, and stainless steel. MIG welding works well on materials that are easy to process and don’t require high precision.
- TIG Welding: Ideal for thin metals like aluminum and stainless steel, especially when the project requires a high level of precision and an aesthetic finish.
Project Requirements
- MIG Welding: Choose MIG welding for projects that require speed, strength, and durability, especially when working with larger or thicker parts. It’s also the better choice for mass production and when you need to work with various types of metals.
- TIG Welding: TIG welding is the go-to choice for projects that require precision, delicate work, or a high-quality appearance. It's perfect for intricate designs, thin materials, and when you need flawless, aesthetically pleasing welds.
Skill Level
- MIG Welding: MIG welding is easier for beginners to learn, as the process is more forgiving and requires less manual dexterity. The automatic feeding of the electrode wire makes it a good option for those just starting in the welding world.
- TIG Welding: TIG welding is more complex and requires more practice and skill. It’s better suited for experienced welders who can manage the dual task of controlling the torch and feeding the filler rod simultaneously.
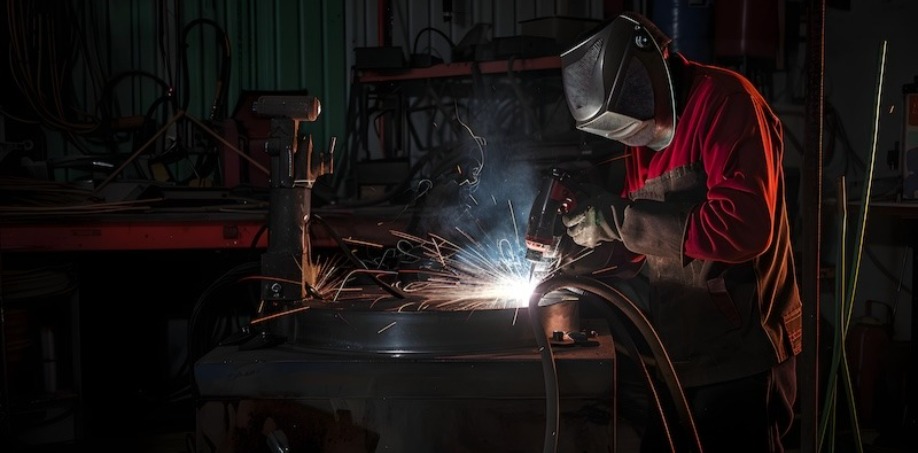
In the end, deciding between MIG and TIG welding depends on your specific project needs. If speed, strength, and ease of use are your priorities, MIG welding is the way to go. However, if you require precision, cleanliness, and aesthetic welds, TIG welding is the better choice. Whether you're working on large-scale industrial projects or fine, detailed artistic designs, the right welding technique will ensure that your work is strong and durable. If you are in need of MIG or TIG welding supplies, give our sales team a call at 877-446-4352.